Good high temperature oxidation resistance to 2000°F
High temperature stability for moderate strength applications- Good oxidation and carburization resistant to 2000°F
- Resistance to moderate sulfidation and nitriding
- Economic alternative to high temperature nickel alloys
- 310SS chemistry & specifications
- Features & benefits of 310SS weld neck flanges
- Datasheet for 310 stainless steel
Designed for high temperature applications, 310 stainless steel weld neck flanges provide high temperature oxidation resistance to 2000°F under mild cyclic conditions. An economic alternative to nickel alloys like alloy 330 or Inconel, 310 flanges provide slightly less strength and temperature resistance – but at a significantly lower price point. Alloy 310 can be used in moderately caburizing, moderately oxidizing, nitriding, cementing and thermal cycling applications when not used at the maximum service temperature. 310SS weld neck flanges also have good resistance to sulfidation and other forms of hot corrosion. Although primarily known for its high temperature properties, 310 stainless steel also provides excellent performance at cryogenic temperatures, with toughness down to -450F. Though 310 weld neck flanges are ideal for high temperature use, they should not be exposed to the severe thermal shock of repeated liquid quenching or where aqueous corrosive contaminants are present.
Benefits
- High temperature resistance.
- Excellent resistance to oxidation under mildly cyclic conditions.
- Good resistance to sulfidation and atmospheres where sulfur dioxide gas is encountered at elevated temperatures.
- Good resistance to thermal fatigue.
- Excellent toughness to cryogenic temperatures of -450°F.
- Low magnetic permeability.
- Good ductility and weldability.
Applications
- Thermal processing and high temperature furnaces rely on 310 flanges for their high temperature and oxidation resistance in minor cyclic conditions.
- 310SS weld neck flanges are commonly used in the petrochemical industry for their ability to provide resistance to moderately carburizing atmospheres.
- The high temperature properties of 310 weld neck flanges make them ideal for ore processing, steel plants, power generation, and sintering.
- Cryogenic structures often use 310 stainless steel flanges for their strength at -450°F and low magnetic permeability.
310 Stainless Steel Properties | |
Tensile Strength (ksi) | 70 |
Yield Strength (ksi) | 30 |
Rockwell B Hardness | 95 |
Density (lb/in3) | 0.285 |
Electrical Resistivity (Microhm-in at 68°C) | 30.7 |
Modulus of Elasticity (x 106 psi) | 28.5 |
Thermal Conductivity at 212°F (BTU/hr/ft2/ft/°F) | 8.0 |
Resources: Flange Dimensions, Flange Bolting Chart
Alloy 310 Bolt Types: Blind Flanges, Lap Joint Flanges, Slip On Flanges, Socket Weld Flanges, Threaded Flanges, Weld Neck Flanges
310 Stainless Steel Chemistry & Specifications
310SS Specifications: AMS 5521, AMS 5651, ASME SA 240, ASME SA 312, ASME SA 479, ASTM A 240, ASTM A 276, ASTM A 276 Condition A, ASTM A 276 Condition S, ASTM A 312, ASTM A 479, EN 10095, UNS S31008, UNS S31009, Werkstoff 1.4845
310SS Weld Neck Flange Features & Benefits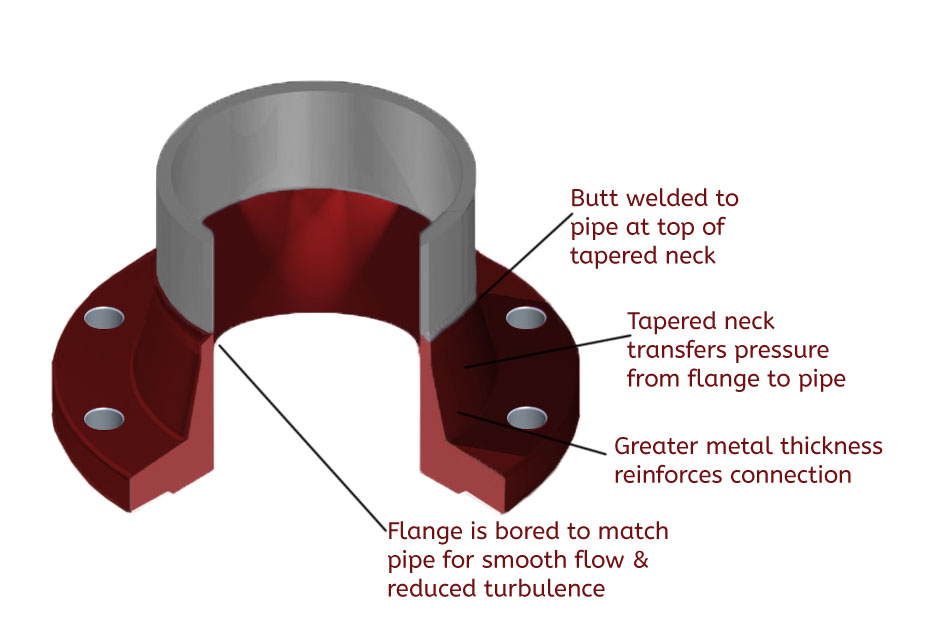
310 weld neck flanges are best for hazardous, high pressure applications. Weld neck flanges are easily identified by their long tapered neck. The inside of the flange is bored to match the inside diameter of the pipe in order to ensure there is no restriction in flow and also to prevent turbulence at the joint. The tapered neck provides thicker metal at the flange joint, while the neck narrows down gradually to meet the pipe where it is butt welded to the pipe. This design helps to transfer stress from the flange to the pipe, as well as diminish stress concentration at the base of the flange connection.
310SS weld neck flanges are ideal for critical applications involving high pressure, sub-zero and elevated temperatures, as well as in conditions where fluctuations cause pipe expansion/contraction.
Key Feature: Ideal for high presure applications.
Weld Neck Flange Advantages
- Ability to withstand high pressure – since pipe is welded to the neck of the flange, stress is transferred to the pipe.
- The beveled end that, when connected to a pipe, creates a trough for a strong weld.
- Most versatile flange in the ASME stable of flanges.
Weld Neck Flange Disadvantages
- More advanced welding skill is needed for installation. The inside weld must be smooth to reduce friction and the outside weld must meet code criteria.
Uses
- Severe conditions that include high-pressure, high-cyclic and hazardous fluid applications.
- Fitting-to-fitting fabrication where the flange is welded directly to a fitting, such as an elbow, without the need for a short piece of pipe, as would be required with a slip-on flange.