An engineered stainless steel known for its high yield strength & decent corrosion resistance
- High Strength - About 2x stronger yield than 316 stainless steel
- Super Duplex - Decent general corrosion & cracking resistance
- Duplex Grades: Duplex 2205, Super Duplex 2507, Zeron 100
- Weld neck flange features and benefits
- Datasheets for Super Duplex 2507 and Duplex 2205
Duplex 2205 and Super Duplex 2507 stainless steel weld neck flanges are characterized by their high yield strength, which is twice that of the annealed yield strength of typical austenitic stainless steels, like 304 and 316 stainless steel weld neck flanges. Because of this, Duplex 2205 and Super Duplex 2507 steel are some of the most common grades of duplex used for weld neck flanges with Super Duplex 2507 weld neck flanges being the more corrosion resistant grade of the two.
Super Duplex 2507 weld neck flanges improved corrosion resistance lends itself well too applications prone to stress-corrosion cracking, crevice corrosion, pitting, erosion and general corrosion. Because of the properties of Duplex and Super Duplex stainless steel weld neck flanges are often used in chemical processing, petrochemicals, power industry and seawater equipment.
Usage of both Duplex and Super Duplex stainless steel should be limited to temperatures below 570° F as extended elevated temperature exposure can embrittle this material.
The most common grades of Duplex flanges are Duplex 2205 and Super Duplex 2507. Gain more insight on these two grades by accessing our Duplex 2205 and Super Duplex 2507 overviews or by contacting our engineering experts.
Resources: Duplex & Super Duplex Torque Specs, Flange Dimensions, Flange Bolting Chart
Flange Types Available: Blind Flanges, Lap Joint Flanges, Slip On Flanges, Socket Weld Flanges, Threaded Flanges, Weld Neck Flanges
Duplex Weld Neck Flange Grades, Chemistry & Specifications
Duplex Alloy 2205
Duplex 2205, UNS S32205, is a stainless steel material, whose “Duplex” name is derived from the mixed microstructure which contains roughly equal portions of ferrite and austenite. This grade is the most popular variety and this two-phase material is a significant upgrade from 316 stainless steel in terms of both yield strength and corrosion resistance.
Duplex 2205 Specifications: ASME SA 182, ASME SA 240, ASME SA 479, ASME SA 789, ASME SA 789 Section IV Code Case 2603, ASTM A 240, ASTM A 276 Condition A, ASTM A 276 Condition S, ASTM A 479, ASTM A 790, NACE MR0175/ISO 15156, NORSOK MDS D45 Grade F51, UNS S31803, UNS S32205, W. NR./EN 1.4462, Werkstoff 1.4462 Duplex
Super Duplex Alloy 2507
Super Duplex 2507, UNS S32750, is a two-phase stainless steel and is particularly well suited for use in environments such as warm chlorinated seawater and acidic, chloride containing media. It has similiar properties to Duplex 2205 but is more corrosion resistant and performs well in moderately corrosive environments.
Super Duplex 2507 Specifications: EN 10216-5, ASTM A789; A790, ASTM A182 ASTM A182, ASTM A815, ASTM A240, EN 10088-2, ASTM A479, EN 10088-3 EN 10088, ISO 15156-3, NACE MR0175, Werkstoff 1.4410 S.Duplex
Zeron 100 / F55:
Zeron 100, UNS 32760, is commonly know as F55, which is a slight varient of Super Duplex 2507. This alloy is well suited or seawater applications.
Zeron 100/F55 Specifications: ASTM A 182, ASTM A 182 (Grade F55), ASTM A 240, ASTM A 276, ASTM A 473, ASTM A 479, ASTM A 790, ASTM A 815, ASTM A314, NORSOK MDS 055, UNS S32760, W. Nr./EN 1.4501, Werkstoff 1.4501
Mechanical Data
Duplex Steel Weld Neck Flange Features & Benefits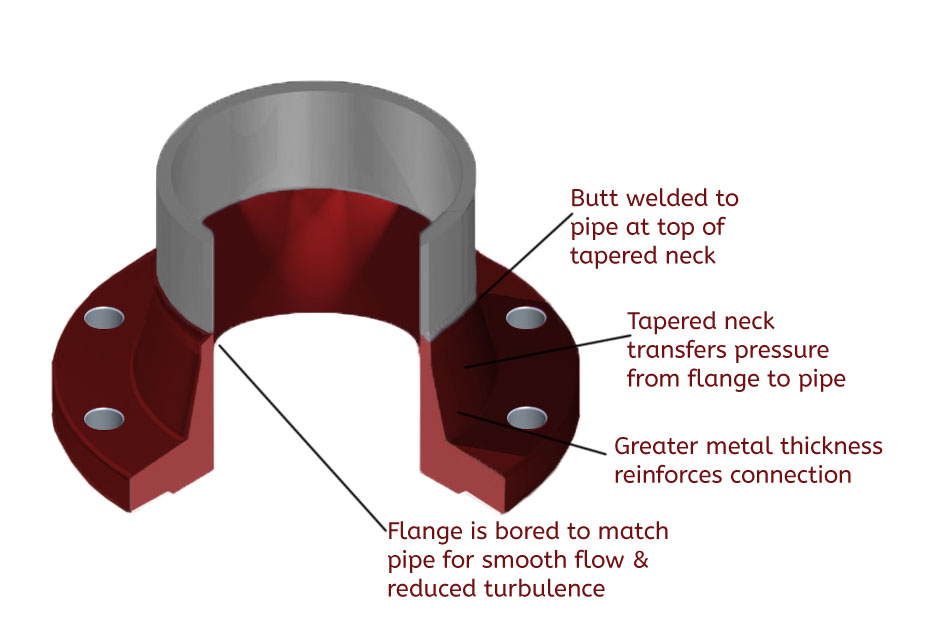
Duplex weld neck flanges are best for hazardous, high pressure applications. Weld neck flanges are easily identified by their long tapered neck. The inside of the flange is bored to match the inside diameter of the pipe in order to ensure there is no restriction in flow and also to prevent turbulence at the joint. The tapered neck provides thicker metal at the flange joint, while the neck narrows down gradually to meet the pipe where it is butt welded to the pipe. This design helps to transfer stress from the flange to the pipe, as well as diminish stress concentration at the base of the flange connection.
Duplex and Super duplex weld neck flanges are ideal for critical applications involving high pressure, sub-zero and elevated temperatures, as well as in conditions where fluctuations cause pipe expansion/contraction.
Key Feature: Ideal for high presure applications.
Weld Neck Flange Advantages
- Ability to withstand high pressure – since pipe is welded to the neck of the flange, stress is transferred to the pipe.
- The beveled end that, when connected to a pipe, creates a trough for a strong weld.
- Most versatile flange in the ASME stable of flanges.
Weld Neck Flange Disadvantages
- More advanced welding skill is needed for installation. The inside weld must be smooth to reduce friction and the outside weld must meet code criteria.
Uses
- Severe conditions that include high-pressure, high-cyclic and hazardous fluid applications.
- Fitting-to-fitting fabrication where the flange is welded directly to a fitting, such as an elbow, without the need for a short piece of pipe, as would be required with a slip-on flange.